Between the body work on the truck , redesign on the backhoe forks, and the new box scraper I plan on making for the ATV, I must have dragged my welding sh!t in and out of the garage 20 times. Time to build a welding cart that carries the welder, the tha Argon tank, the TIG torch, grounding clamps, filler metals, helmet, glasses, clamps, ... and anything else I can fit. Using a mix of old and new, this baby will be an All Terrain cart that is so over built it's not funny.




The bars in the back will be the handle for the cart , the bars up front will hold the welder at an angle that nake it easier to read the display, and there will be 1 or more drawers underneath withe side access.
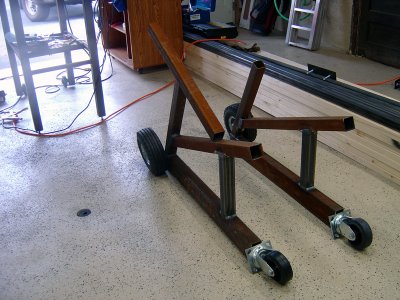
Oops, ran out of Argon...